Bau einer Demonstrationsanlage zur Rückgewinnung fluorierter Monomere aus Fluorpolymerabfällen
Nachhaltiges Verfahren hält wertvolle Rohstoffe im Kreislauf
Umweltentlastung
Umweltentlastung
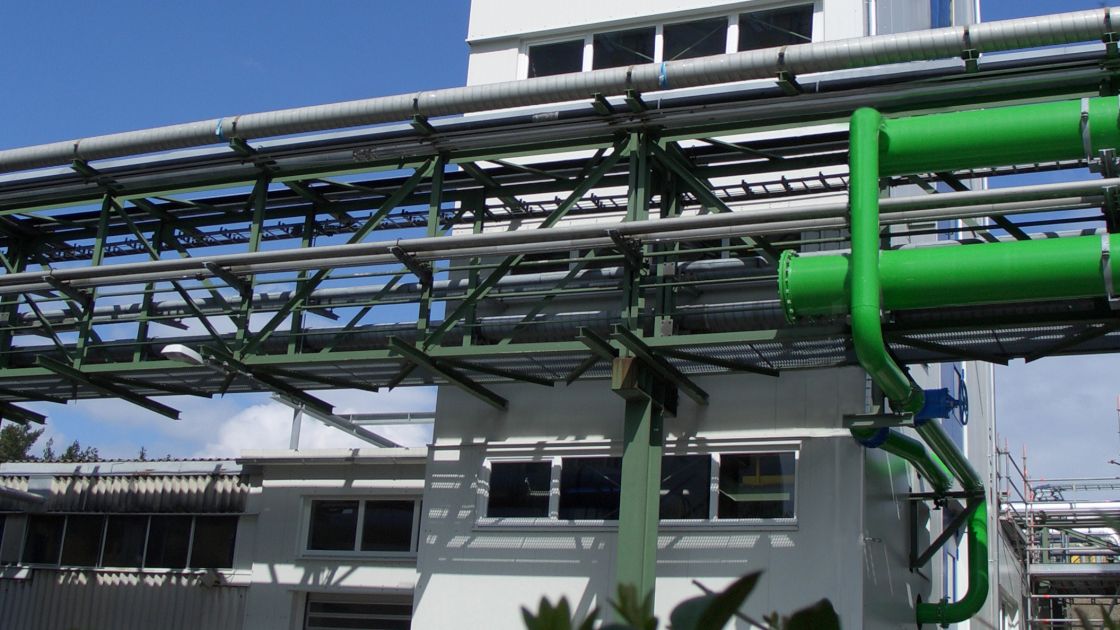
Kurzbeschreibung
Die Dyneon GmbH, eine 100-prozentige Tochtergesellschaft der 3M und Teil der Advanced Materials Division, ist einer der führenden Fluorpolymerhersteller der Welt und verantwortet in seiner Firmenzentrale in Burgkirchen (Bayern) die Entwicklung, Herstellung und Vermarktung von Fluorpolymeren. Das Produktportfolio umfasst Fluorelastomere, Fluorthermoplaste, Polytetrafluorethyle (PTFE) und Kunststoff-Additive. Durch ihre hohe thermische und chemische Beständigkeit eignen sich die Materialien für zahlreiche Hightech-Anwendungen, beispielsweise in der Automobilindustrie und Architektur.
Ohne vollfluorierte Polymere wären zahlreiche alltägliche Gebrauchsgegenstände nicht möglich, denn sie machen das Leben in vielerlei Hinsicht bequemer und sicherer. In Europa werden jedes Jahr ca. 34.000 Tonnen Polytetrafluorethen (PTFE) und PTFE-Compounds verarbeitet. Allerdings: Für PTFE-Compoundabfälle sowie für PTFE-Abfälle aus dem Post-Consumer-Bereich existierte bisher weltweit kein stoffliches, qualitativ hochwertiges Recyclingkonzept. Sie wurden entweder in Verbrennungsanlagen thermisch verwertet oder deponiert. Ein innovatives Recyclingverfahren von Dyneon macht es möglich, dieses erhebliche Potenzial an Wertstoffen zu nutzen und es wieder in den Produktionskreislauf zurückzuführen – und das gänzlich ohne Qualitätseinbußen.
Die Pilotanlage der Dyneon GmbH spaltet mit Hilfe eines Pyrolyseverfahrens die PTFE-Abfälle wieder in seine Ausgangsmonomere auf. Nach der Konditionierung (Zerkleinerung) und einem Waschprozess werden die PTFE-Abfälle bei Temperaturen zwischen 400 Grad Celsius und 700 Grad Celsius in einem Pyrolysereaktor vollständig zersetzt. Hierbei kommen zwei unterschiedlichen Reaktorkonzepte zum Einsatz: Ein Wirbelschicht- und ein Rührbettreaktor. Aus den Reaktionsgasen werden die Monomere Tetrafluorethen (TFE) und Hexafluorpropen (HFP) zurückgewonnen. Die Monomere werden destillativ gereinigt und lassen sich danach wieder zu PTFE polymerisieren. Das Material kann anschließend ohne Qualitätseinbußen in der Produktion für unterschiedliche Anwendungen wieder zum Einsatz kommen. Die neue Anlage ist zunächst für eine Kapazität von jährlich ca. 500 Tonnen PTFE-Abfällen ausgelegt.
Mit dem neuen Recyclingverfahren können pro Kilogramm recyceltem TFE 70 Prozent an Energie und 61 Prozent CO2-eq-Emissionen eingespart werden. Bei einer Jahreskapazität von 500 Tonnen entspricht dies einer Einsparung von 19 Millionen Kilowattstunden und 2.850 Tonnen CO2-eq. Die Umwelt profitiert somit nachhaltig von dem intelligenten Up-Cycling, das den Weg in eine ökoeffiziente Kreislaufwirtschaft (circular economy) weist. Dyneon verfügt dazu über klar definierte Abläufe, um die Abfallströme gemäß dem deutschen Kreislaufwirtschaftsgesetz und EU-Verordnung individuell zu betrachten, einzustufen und zu prozessieren. Verarbeiter und Hersteller aus mehreren EU-Ländern beteiligen sich bereits am Up-Cycling.