Energieeinsparungen durch Bandgießen von Leichtbaustählen (EnBaL)
Neues Gießverfahren für Stahl ermöglicht Energieeinsparungen im Walzwerk und zugleich Kraftstoffeinsparungen durch neuer Leichtbaustähle
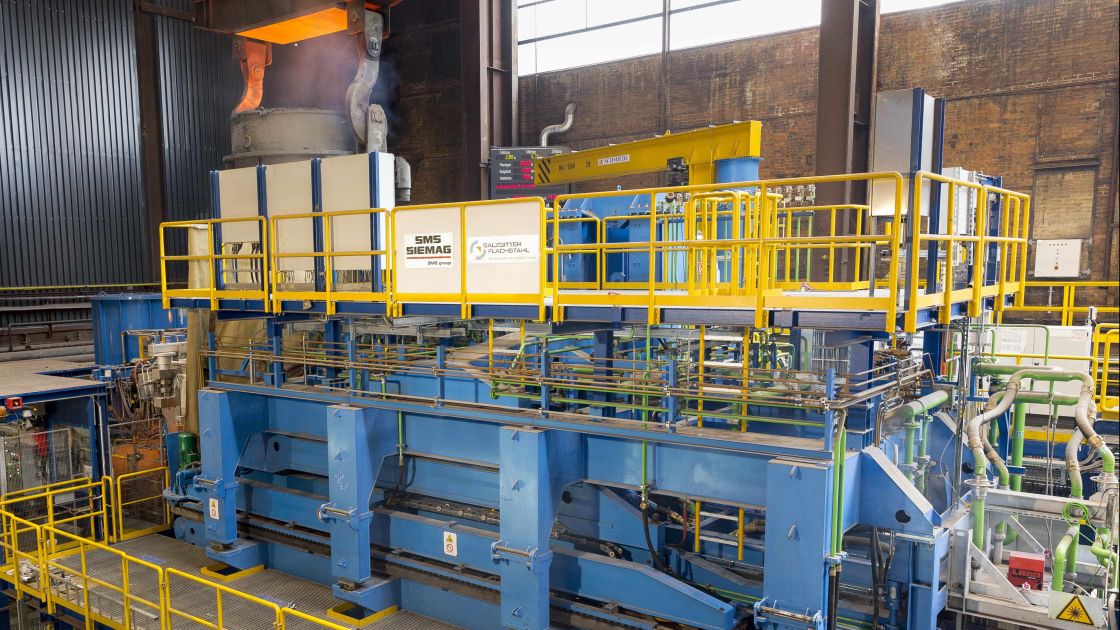
Kurzbeschreibung
Die Salzgitter Flachstahl GmbH erzeugte mit über 4.700 Mitarbeitern etwa 4,4 Millionen Tonnen Rohstahl pro Jahr (2013), die in Form von Warmbreitband, Bandstahl, Bandblech, und Feinblechen Verwendung in der Automobilindustrie, bei Röhrenherstellern oder der Bauindustrie finden.
Ziel des kürzlich abgeschlossenen Umweltinnovationsvorhabens der Salzgitter Flachstahl GmbH waren Energieeinsparungen und geringere CO2-Emissionen durch Anwendung eines völlig neuen Gießverfahrens im Stahlwerk, welches erhebliche Energieeinsparungen beim Warmwalzen ermöglicht und das zugleich Voraussetzung für die Erzeugung neuartiger Leichtbaustähle ist, die bei Verwendung im Fahrzeugbau zu weiteren großen Energieeinsparungen führen.
Bisher wird der flüssige Stahl zur Herstellung warmgewalzter Bleche mittels Strangguss zu bis zu 30 Zentimeter dicken Brammen gegossen, die zunächst zur Erstarrung auskühlen müssen, bevor sie anschließend wieder mit hohem Energieaufwand auf Walztemperatur (>1.150 Grad Celsius) erhitzt und mit ebenfalls hohem Energieaufwand auf die Zieldicke gewalzt werden.
Beim Bandgießverfahren wird der Stahl dagegen direkt zu einem 8–15 Millimeter dicken Stahlband vergossen, welches unmittelbar dem Walzwerk zugeführt werden kann. Durch den weitgehenden Entfall des Wiedererhitzens und die geringere Arbeit, die zur Erreichung der Zieldicke benötigt wird, sinkt der Energiebedarf für das Warmwalzen um bis zu 70 Prozent.
Zielprodukt der Demonstrationsanlage war ein neu entwickelter Leichtbaustahl (HSD-Stahl), der aufgrund seiner Legierungszusammensetzung nicht mit dem herkömmlichen Stranggussverfahren verarbeitet werden kann. Durch seine einzigartige Kombination aus hoher Festigkeit und guter Umformbarkeit eröffnet der HSD-Stahl neue Einsatzmöglichkeiten für Leichtbaukonstruktionen und ermöglicht so über seine Nutzungszeit weitere erhebliche Energieeinsparungen und CO2-Minderungen.
Im Rahmen des Vorhabens errichtete die Salzgitter Flachstahl GmbH eine industrielle Pilotanlage zur Herstellung von 1.000 Millimeter breiten und 8–15 Millimeter dicken Vorbändern am Standort Peine. Zudem wurde eine ehemalige Walzanlage am Standort Salzgitter so umgerüstet, dass sie das Vormaterial aus der Bandgießanlage zu marktfähigen Stahlbändern auswalzen kann. Mit der Demonstrationsanlage konnte die industrielle Anwendbarkeit des Bandgießverfahrens erfolgreich nachgewiesen werden. Das große Energiesparpotential des Bandgießverfahrens konnte aufgrund der räumlichen Trennung der beiden Anlagenteile allerdings noch nicht ausgeschöpft werden. Das wird erst mit einer zukünftigen Erweiterung der Anlage um ein „Inline-Walzwerk“ möglich sein, für die das vorliegende Vorhaben die Grundlage bereitet hat.
Im Rahmen eines vom BMBF geförderten wissenschaftlichen Begleitvorhabens wurde ökobilanziell untersucht, wie vorteilhaft der HSD-Stahl gegenüber den bisher industriell verfügbaren hochfesten Stahlsorten ist. Der kumulierte Energieaufwand (KEA) für die Herstellung von HSD-Stahl über das Bandgießverfahren ist bis zu 18 Prozent geringer als der für andere hochfeste Stähle; das Treibhauspotential (GWP) des HSD-Stahls ist sogar um bis zu 40 Prozent geringer. Bei zusätzlicher Berücksichtigung der Umweltentlastungen in der Nutzungsphase des HSD-Stahls, z.B. bei deren Verwendung im Automobilbau, können die CO2-Emissionen sogar um 4,8 Kilogramm pro Kilogramm eingesetzten HSD-Stahls gemindert werden.
Das Bandgießverfahren ist generell für alle Anlagen anwendbar, die flüssigen Stahl zu warmgewalzten Blechen verarbeiten, setzt allerdings einen weitgehenden Umbau der bestehenden Stranggussanlagen und Warmwalzwerke voraus. Der mit dem Bandgießverfahren hergestellte HSD-Stahl kann in allen Bereichen eingesetzt werden, in denen sowohl sehr hohe Festigkeiten als auch eine sehr gute Umformbarkeit des Stahls gefordert sind.