Modulare Fertigungslinie zur energieeffizienten und ressourcenschonenden Produktion von Stahlgussteilen (Modulcast) in kleinen und mittleren Serien
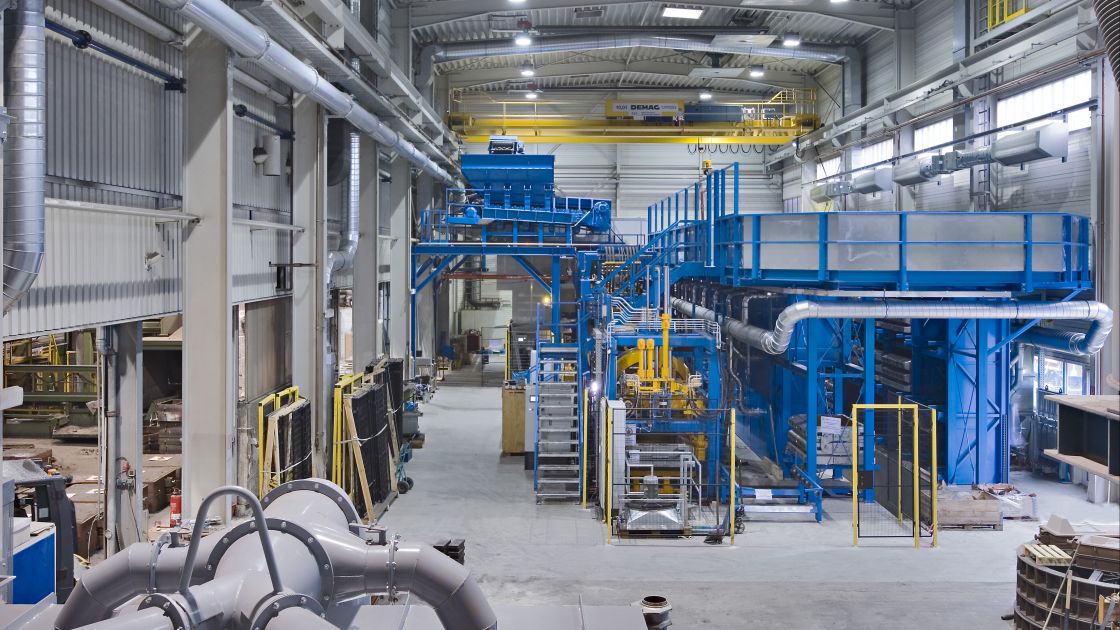
Kurzbeschreibung
Die Friedrich Lohmann GmbH ist ein Unternehmen, das an zwei Standorten in Witten Blech- und Stabstahlprodukte, hitzebeständige und verschleißfeste Edelstahlgussformen sowie Schweissverbundkonstruktionen produziert. Die Hauptanwendungen liegen in den Branchen Automotive, Maschinenbau, Werkzeugbau und Windkraft. Mit ihren Produkten erreicht das Unternehmen eine weltweit führende Marktposition.
Bislang sind Fertigungslinien in Gießereien statisch angelegt. Alle Formkästen werden in einer Linie per Hallenkran angefahren, abgegossen und nach Entnehmen des Gussstücks wieder hinten in der Formanlage eingereiht. Während diese Art der Formanlage für größere Gießserien mit gleichartigen Bauteilen und Werkstoffen gut geeignet ist, sind sie für kleine und mittlere Serien nur bedingt geeignet, da auf Grund unterschiedlicher Geometrien und Werkstoffe langsam erstarrende Gussstücke die gesamte Fertigungslinie blockieren. Zeitverzögerungen bis zum Abgießen des letzten Formkastens können nur durch höhere Gießtemperaturen kompensiert werden. Dadurch entstehen Energie- und Abbrandverluste (Metallverlust beim Schmelzen). Außerdem kann weder eine Absaugung der Abluft noch eine Nutzung der Abwärme erfolgen.
Das Unternehmen wird eine neuartige modulare Fertigungslinie für ein ressourcen- effizientes Formen und Gießen von kleinen und mittleren Serien mit Losgrößen von
1 bis 500 Stück errichten. Das Konzept basiert auf einer nicht mehr statischen, sondern flexiblen, programmgesteuerten Gießlinie in Hochregallagerform. Die Steuerung sucht je nach Werkstoff, Gießtemperatur und Gewicht die passenden Formkästen heraus. Die Formen werden in einer vorbestimmten energie- und fertigungsoptimalen Reihenfolge bereitgestellt, abgegossen und anschließend in freie Plätze umgelagert. Die Abluft wird mit Filtern gereinigt (nicht Bestandteil des geförderten Vorhabens) und die Abwärme mit Hilfe eines Wärmetauschers zurückgewonnen und zur Beheizung der Produktionshalle eingesetzt.
Der Stromverbrauch kann um ca. 693.000 Kilowattstunden pro Jahr reduziert werden. Dadurch verringern sich die CO2-Emissionen um ca. 415 Tonnen CO2 jährlich. Weiterhin ergeben sich erhebliche Reduktionen des Abbrands, des Ausschusses und der Staubemissionen.