Emissionsminderungsmaßnahmen in der Sekundärhütte (RWN)
Emissionsminderung in der Hüttenindustrie
Umweltentlastung
Umweltentlastung
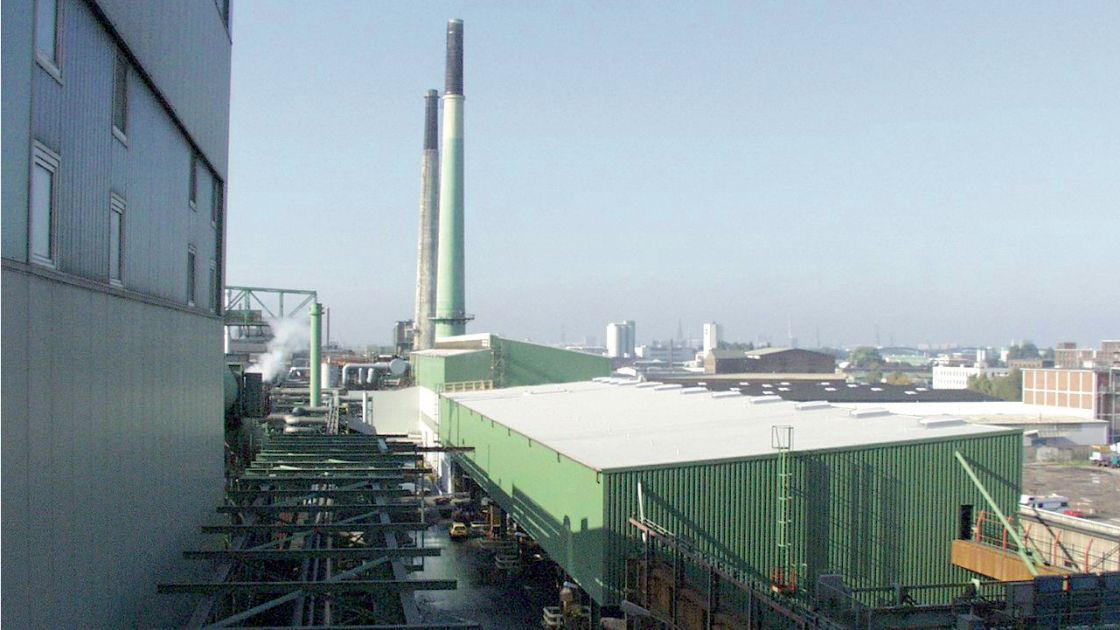
Kurzbeschreibung
Die Aurubis AG (ehemals Norddeutsche Affinerie AG) ist Europas größter Kupferproduzent und der weltweit größte Kupferrecycler. Am Standort Hamburg gewinnt das Unternehmen u.a. Kupfer aus Kupfererzkonzentraten, Altkupfer und Recycling-stoffen und verarbeitet dies in eigenen Anlagen zu Halbzeug wie beispielsweise Draht weiter.
In der Sekundärhütte (RWN) werden komplexe sekundäre Rohstoffe (kupfer-, edelmetall-, blei- und nickelhaltige Hüttenzwischenprodukte, Recyclingmaterialien und Abfälle zur Verwertung) verarbeitet, die weltweit eingekauft oder von der Aurubis AG selbst produziert werden. Die Halle, in der sich die Produktionsanlagen befinden, ist etwa 80 Meter lang und schloss sich vor dem Projekt an einen offenen Zwischenproduktplatz an.
Beim Ein- und Ausgießen des geschmolzenen Materials treten staub- und schwer-metallhaltige Emissionen auf, die früher nur ungenügend abgesaugt und gereinigt werden konnten. Die Folge waren Belastungen der Innenluft und der Austritt von Emissionen über das Hallendach in die Außenluft. Das Absaugen der gesamten Halle war technisch und ökologisch nicht sinnvoll. Ziel des Fördervorhabens war es, ein neues Verfahren in die Anwendung zu bringen, um die diffusen staub- und schwermetallhaltigen Emissionen zu erfassen und abzuscheiden.
Um ein wirkungsvolles Erfassen mit möglichst minimalem Absaugvolumen zu erreichen, wurden die Produktionsanlagen nach dem sogenannten "Haus-in-Haus-Konzept" kleinräumig umbaut. Absaugvorrichtungen erfassen und reinigen die diffusen Emissionen nun direkt an der Quelle. Die erforderliche Absaugmenge wurde regeltechnisch optimiert. Das Absaugen erfolgt zielgerichtet und wird angepasst an den Produktionsablauf gesteuert. Über den gesamten Zwischenproduktplatz wurde die Konverterhalle so verlängert, dass alle festen Stoffe innerhalb des Hallendachs umgeschlagen werden können. Des Weiteren verlegte man die Gießvorgänge des schmelzflüssigen Materials unter Hauben und kann sie nun von außen steuern. Die Reinigung der erfassten Haubenabgase erfolgt mit Hilfe von Gewebefilteranlagen.
Die bisher auftretenden Emissionen an Fein- und Metallstäuben in die Außenluft konnten durch die Einhausung und das zielgerichtete Absaugen erheblich vermindert werden. Die Überdachung des Zwischenproduktplatzes bewirkt, dass die beim Lagern und beim Umschlag auftretenden Emissionen in die Umgebungsluft weitgehend vermieden werden. Insgesamt werden durch die Installation optimierter und angepasster Erfassungsanlagen stündlich 200.000 Kubikmeter Hallenluft abgesaugt. Dies ist etwa ein Viertel des Abluftvolumenstromes, der bei einer vollständigen Hallenabsaugung anfallen würde. Die gezielten Einhausungsmaßnahmen sparen somit gegenüber der Alternative einer vollständigen Hallenabsaugung große Mengen an Energie. Im Vergleich zum Ausgangszustand ist der jährliche Energiebedarf durch die zusätzlichen Absaugeinrichtungen jedoch um 1.600 Megawattstunden angestiegen.
Der im Gewebefilter abgeschiedene und im Staubsammelbunker anfallende Staub ist ein Zwischenprodukt für die Metallgewinnung. Er wird direkt in der Hütte weiterverarbeitet. Gleiches gilt genauso für die metallhaltige Schlacke, das Werkblei und den Kupferbleistein. Abfälle fallen in Form verbrauchter Filtermaterialien an.
Die Arbeitsplatzsituation für die Mitarbeiter konnte deutlich verbessert werden, denn die Arbeitsplatzbelastung durch Cadmium und Arsen im Schwebstaub ist deutlich vermindert. Aufgrund der verminderten Emissionen kann die Anlage die ab 2012 geltenden Zielwerte der Luftqualitätsrichtlinie der EU (Immissionsbelastung) für Cadmium (5 Nanogramm/Kubikmeter) und Arsen (6 Nanogramm/Kubikmeter) schon jetzt einhalten.
Das Pilotprojekt zeigt, mit welchen Maßnahmen die Hüttenindustrie staub- und schwermetallhaltige Emissionen deutlich vermindern kann, um die künftige EU-Luftqualitätsrichtlinie zu erfüllen. Die Maßnahmen sind auf verschiedene Anlagenarten mit Schmelzprozessen übertragbar und wurden daher auch bei der Bearbeitung des BVT-Merkblattes der Nichteisen-Metallindustrie berücksichtigt.