Energieeffiziente automatisierte Kommissionierungsanlage für Konstruktionsvollholz (KVH-Flächenlager)
Die erste automatisierte Kommissionierungsanlage für Konstruktionsvollholz und Brettschichtholz spart Energie und schont die Umwelt
Umweltentlastung
Umweltentlastung
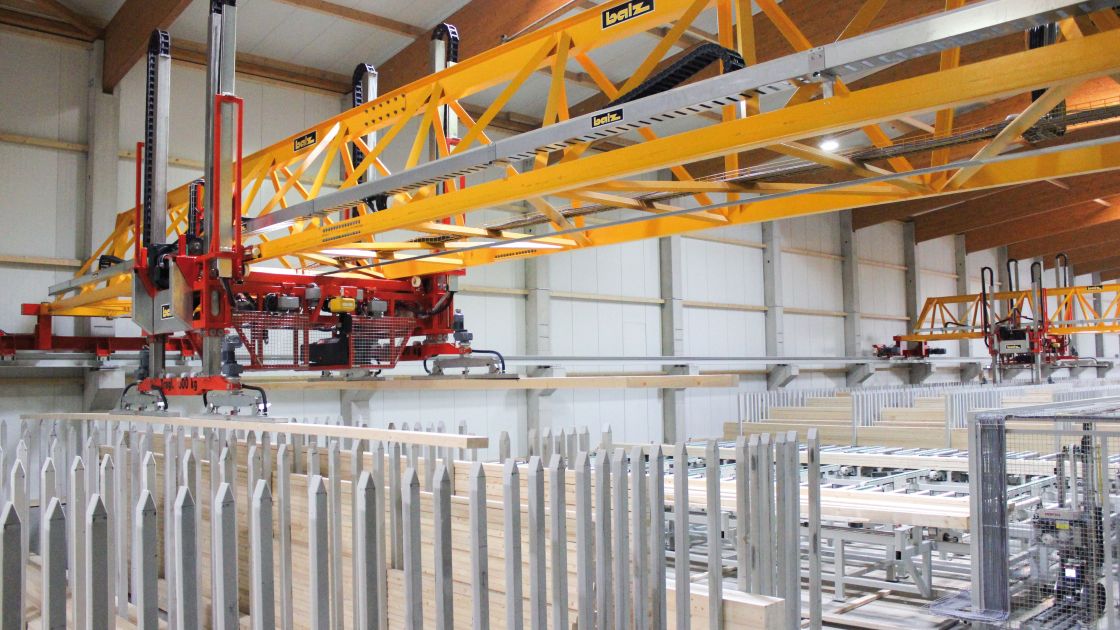
Kurzbeschreibung
Die Holzgroßhandlung Karl Ahmerkamp Vechta GmbH & Co. KG wurde 1964 gegründet. An ihrem Stammsitz in Vechta betreibt das Unternehmen ein automatisches Lager zur Kommissionierung von Konstruktionsvollholz und Brettschichtholz. Im Holzgroßhandel wurden bisher zur Lagerhaltung von Konstruktionsvollholz und Brettschichtholz Hochregal- und Blocklager genutzt. Der innerbetriebliche Transport der Hölzer bei der Warenein- und Warenauslagerung erfolgte mit dieselbetriebenen Gabelstaplern. Die bisherige Art der Kommissionierung erforderte, dass zunächst der gesamte Inhalt eines Regalfaches des Hochregallagers zum vorgesehenen Kommissionierplatz zur Zwischenlagerung transportiert werden musste. Auf dem Kommissionierplatz wurde die benötigte Anzahl an Hölzern händisch aus dem soeben geholten Paket (Inhalt des Regalfaches) entnommen. Im Anschluss mussten die verbliebenen Reststücke wieder zurück ins ursprüngliche Fach des Hochregallagers gebracht werden. Zum Schutz der Ware wurden die Kommissionspakete im Anschluss händisch mit Plastikfolie umwickelt.
Ziel des Vorhabens der Karl Ahmerkamp Vechta GmbH & Co. KG war die Automatisierung der Lagerhaltung und Kommissionierung von Konstruktionsvollholz und Brettschichtholz. Dadurch sollte die Effizienz der Lagerhaltung verbessert und der Energieverbrauch deutlich gesenkt werden. Realisiert wurde dieses Ziel durch die erstmalige großtechnische Umsetzung eines elektrisch betriebenen vollautomatischen Kran- und Saugsystems in Verbindung mit einem Flächenlager. Innovativ ist hierbei auch die softwareseitige Optimierung der Fahrwege und der Stapelbildung, so dass die Fahrwege insgesamt minimiert und Leerfahrten vermieden werden.
Ab dem Wareneingang werden die Hölzer durch das automatische Transportsystem aufgenommen. Dieses besteht aus zwei Kransystemen, die wiederum jeweils zwei Saugsysteme zum Anheben der Hölzer besitzen. Bereits bei der Wareneinlagerung optimiert die Planungssoftware für den Wareneingang und -ausgang situationsabhängig mögliche Kombinationen von Ein- und Auslagervorgängen, um Fahrwege zu minimieren, Leerfahrten zu vermeiden und die Produktivität zu erhöhen. Die einzulagernden Hölzer werden entsprechend der Warenein- und -auslagerungssteuerung automatisch an einen geeigneten freien Lagerplatz gebracht. Die Reihenfolge und Anordnung der Hölzer am Warenausgang ist ebenfalls softwareoptimiert, sodass ein umlade-, transport- und verladesicherer Stapel erzeugt wird. Die fertigen Pakete werden durch eine automatische Wickelmaschine materialeffizient in Stretch-Folie verpackt.
Durch die Nutzung von effizienten Motoren (mindestens IE3) und der Rückeinspeisung von Bremsenergie in das System konnten innerhalb des Vorhabens deutliche Energieeinsparungen erzielt werden. Im Rahmen des durchgeführten Messprogramms konnte eine Energieeinsparung in Höhe von 90 Prozent der ursprünglich benötigten Energie nachgewiesen werden. Das entspricht einer Einsparung von 186.642 Kilowattstunden elektrischer Energie pro Jahr. Umgerechnet in CO2 Emissionen führt dies zu einer jährlichen Einsparung von 53.378 Kilogramm CO2, was eine Minderung um 87 Prozent, bedeutet. Durch die materialeffiziente automatische Wickelmaschine werden zusätzlich 1,9 Tonnen Plastikverpackungsmaterial eingespart. Das innovative Verfahren besitzt Modellcharakter und ist auf zahlreiche weitere Unternehmen des Holzhandels übertragbar.