Errichtung einer innovativen, umweltfreundlichen, vollintegrierten und energieoptimierten Umlauf-Spaltanlage zur Herstellung von gewichtsreduzierten Beton-Verbundsystem-Komponenten zur Abfangung von Geländeunterschieden
Umweltentlastung
Umweltentlastung
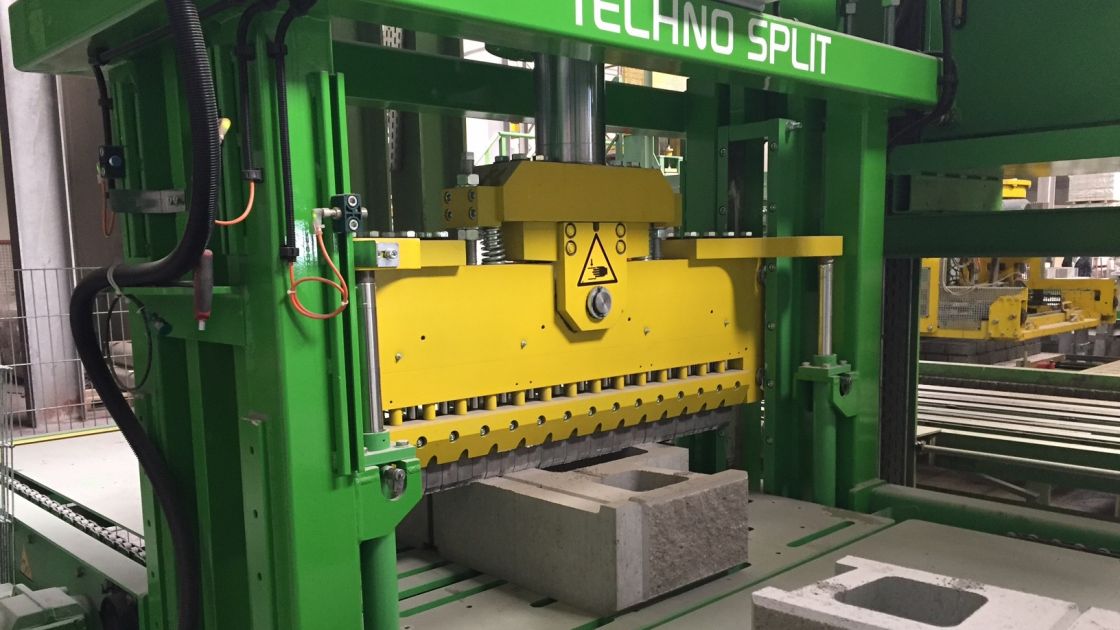
Kurzbeschreibung
Die Betonwerk Brilon GmbH & Co. KG produziert und vertreibt Betonwaren. Nach dem Stand der Technik werden Betonelemente, die zur Nachbearbeitung mittels Spalten vorgesehen sind, in einer Trockenkammer ca. einen Tag lang erhärtet und anschließend zu Paketen gestapelt (Paketierung). So verbleiben sie bis zu zwei Wochen auf dem Lagerplatz. Erst dann hat der Betonkörper eine solche Festigkeit ausgebildet, dass er in einer Spaltanlage mechanisch bearbeitet werden kann. Dazu werden die Betonelemente wieder ausgepackt, entstapelt und einzeln der Spaltanlage zugeführt. Nach dem Spaltprozess sind die Einzelsteine erneut zu Lagen zusammenzuführen, zu verpacken und einzulagern.
Ziel des Vorhabens ist es, Betonhohlsteine in einer neuartigen vollintegrierten Spaltanlage wesentlich ressourcenschonender und zeiteffizienter herzustellen. Die neue Anlage besteht u. a. aus einer klimatisierten Erhärtungskammer, der eigentlichen Spaltanlage und zwei Paketiergeräten. Die Innovation des Vorhabens besteht darin, die Steine ohne ineffiziente Auslagerungsprozesse in einem Kreislaufsystem herzustellen. Die neue Erhärtungskammer sorgt dafür, dass der Vorgang des Aushärtens von zwei Wochen auf rund zwei Tage verkürzt wird. Außerdem entfallen die umfangreichen Zwischenverpackungen sowie die mit der Auslagerung verbundenen, betriebsinternen Transportwege. Die ausgehärteten Betonsteine können nun direkt der Spaltanlage zugeführt werden. Die dafür eingesetzte Prozessteuerung sorgt für eine verbesserte Prozessgleichheit und erlaubt dünnere Wandstärken der Betonsteine.
Mit dem Vorhaben können jährlich mehr als 180 Tonnen Rohmaterial eingespart werden. Zusätzlich können durch den Wegfall der Verpackungen über 1.500 Abdeckhauben, 4.600 Zwischenlagen aus Folien und 34.000 Laufmeter Kunststoffband eingespart werden. Der Energiebedarf reduziert sich jährlich um mehr als 2.000 Kilowattstunden. Daraus ergibt sich eine CO2-Minderung von bis zu 1.235 Kilogramm pro Jahr.