Realisierung eines innovativen und umwelttechnisch herausragenden Investitionsvorhabens im Bereich des industriellen Digitaldrucks (Bedruckung zylindrischer Hohlkörper)
Umweltentlastung
Umweltentlastung
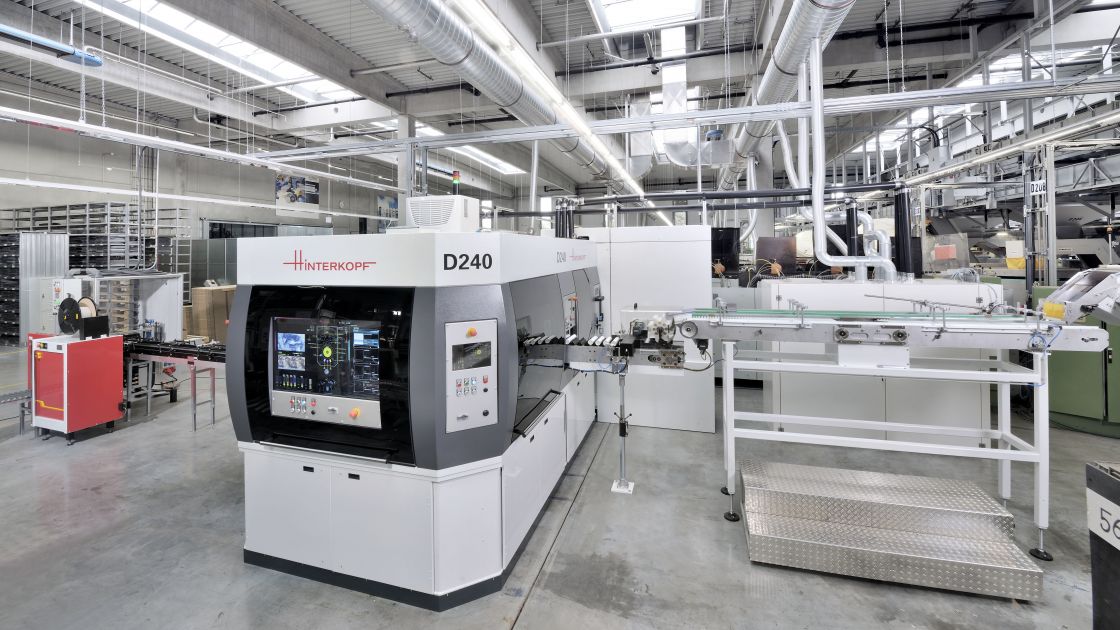
Kurzbeschreibung
Die Ritter GmbH stellt Kunststoff- und Verpackungstechniken her. Zu den wesentlichen Produktbereichen gehören Kartuschen (zylindrische Hohlkörper aus Kunststoff), Medical-Care-Produkte (z.B. Pipettenspitzen) und Baustoffprodukte (z.B. Rasenschutzwaben). Insbesondere die Kunststoff-Kartuschen werden zu Verkaufs- und Werbezwecken bedruckt. Dafür verwendet das Unternehmen das in der Branche übliche Siebdruckverfahren, bei dem die Druckfarbe mit einer Gummirakel durch ein feinmaschiges Gewebe hindurch auf die zu bedruckende Kartusche gedrückt wird. Dieses Verfahren ist jedoch sehr energie-, rohstoff- und zeitintensiv.
Ziel des Vorhabens ist es, das bisherige Siebdruckverfahren durch ein Digitaldruckverfahren zu ersetzen. Beim digitalen Druckverfahren wird das Druckbild direkt von einem Computer in die Druckmaschine übertragen, ohne das es einer Druckvorlage bedarf. Um die 190 mm hohen Kartuschen ausreichend zu bedrucken, werden drei Druckköpfe miteinander kombiniert und synchronisiert. Durch eine rotierende Bewegung werden die Kartuschen an den nahezu starr positionierten Druckköpfen vorbei geführt. Dieser Vorgang wird mehrfach wiederholt, um die gewünschte Druckbildauflösung von bis zu 700 dpi und damit eine hohe Gesamtauflösung zu erhalten.
Die Digitaldruckanlage soll als vollintegrierte Druckanlage aufgebaut werden. Insgesamt sind 16 Stationen vorgesehen, wobei acht Stationen für den Auftrag jeweils einer Farbe eingeplant sind. Weitere Stationen dienen u.a. der Reinigung und Vorbehandlung, der Druckbildkontrolle sowie der Endtrocknung der Kartusche.
Im Vergleich zum bestehenden Siebdruckverfahren können mit dem Vorhaben jährlich drei Tonnen Farbe und bis zu 210 Tonnen Kunststoff für die Kartuschen (High Density Polyethylen, HDPE) eingespart werden. Außerdem kann der Anfall an Sondermüll um 15 Tonnen sowie weitere Abfälle wie Altlacke, Farbreste und Laugen um bis zu 2,4 Tonnen pro Jahr reduziert werden. Die erwartete jährliche Energieeinsparung beträgt 450.332 Kilowattstunden. Die damit verbundene Verringerung des CO2-Ausstoßes beträgt rund 270 Tonnen pro Jahr.