Ressourcenschonende Beschickung von Aluminiumschmelzöfen über ein automatisiertes Batch Intelligence System (BIS)
Digitales Chargenstellungssystem für intelligentes Aluminiumrecycling und CO2-Ersparnis
Umweltentlastung
Umweltentlastung
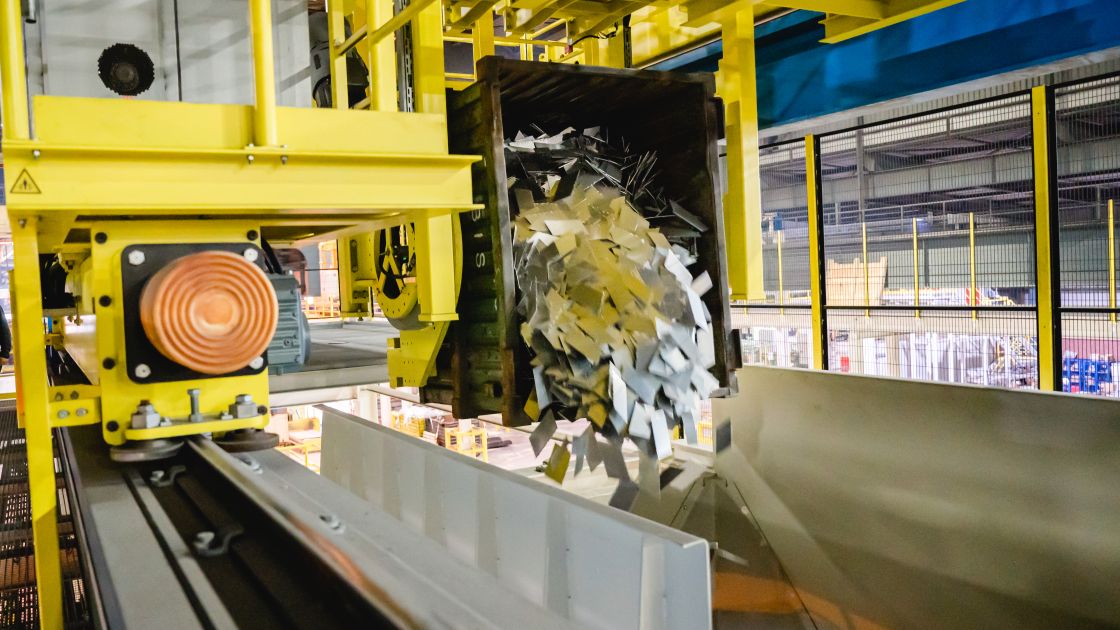
Kurzbeschreibung
Die Aluminium Norf GmbH („Alunorf“) ist ein Joint Venture der Novelis Deutschland GmbH und der Speira GmbH. Mit einer Produktionskapazität von ca. 1,5 Mio. Tonnen kalt- und warmgewalzter Aluminiumbänder im Jahr ist es das größte Aluminiumschmelz- und walzwerk der Welt.
Zur Herstellung der Aluminiumprodukte der Alunorf werden Schrotte unterschiedlichster Legierungen sowie Primärmaterialien eingesetzt. Die Materialien wurden nach dem bisherigen Stand der Technik manuell gelagert und bestimmten Ofenchargen zugeordnet. Die so zusammengestellten Chargen waren daher meist nicht optimal auf die erforderlichen Produktqualitäten eingestellt. Dies führte zu einem Ausbeuteverlust beim Recycling der Schrotte sowie zum dissipativen Verlust von Legierungselementen. Diese Verluste mussten durch eine erhöhte Zugabe von Primäraluminium ausgeglichen werden, was bilanziell zu höherer Umweltbelastung, insbesondere in den Vorketten beitrug.
Ziel des Projektes war eine Steigerung der Energie- und Materialeffizienz sowie die Einsparung von Primäraluminium und Legierungselementen durch die Implementierung eines intelligenten Chargenstellungssystems zur Materialzulieferung, -sortierung, -lagerung sowie zur Chargenvorbereitung und Beschickung der Schmelzöfen. Weiteres Ziel war die Steigerung der Arbeitssicherheit durch automatisierte Transport- und Lagerprozesse.
Die Idee hinter dem „Batch Intelligence System“ (BIS) ist eine weitgehende Automatisierung der Anlagen sowie eine Digitalisierung aller Prozessstufen mithilfe einer intelligenten Software. Alle erforderlichen Daten, wie Gewicht und Legierungszusammensetzung, werden über RFID-Chips auf den Schrottboxen digital erfasst, ausgewertet und zur zentralen Steuerung der Prozesse verwendet. Die Schrottboxen werden über ein automatisches Fördersystem transportiert sowie be- und entladen. Die Software ist dabei in der Lage, Entscheidungen über die Verwendung der Materialien in Echtzeit zu treffen. So wird automatisch die jeweils effizienteste Chargenzusammenstellung realisiert.
Durch das „Batch Intelligence System“ (BIS) können nun große Mengen Primäraluminium durch hochwertig recyceltes Sekundäraluminium ersetzt werden. Beim Ausschöpfen der vollen Produktionsmenge sowie unter Berücksichtigung des variierenden Produktionsmixes können jährlich mindestens 45.000 Tonnen Primäraluminium sowie unterschiedliche Legierungselemente eingespart werden. Dies entspricht einer CO2-Reduzierung von ca. 600.000 Tonnen CO2-Äquivalente.
Das Vorhaben hat einen sehr guten Modellcharakter und ist prinzipiell auf viele Betriebe der Metallbranche, sei es im Aluminium-, sonstigem NE-Metall- oder Stahlbereich, übertragbar. In der gesamten Metallbranche besteht ein großes Interesse daran, Schrotte ihren Eigenschaften entsprechend hochwertiger zu recyclen, um ressourcenintensives Primärmaterial einzusparen.